12.1 Introduction
- In this lecture, we present a brief overview of the refinery supporting processes.
- If we analyze the petroleum refinery, other than hydrocarbon balances, two other components balances need to be considered.
- These are sulphur and hydrogen.
- It is a fact that the refinery has good number of hydrotreaters which needs to be fed with hydrogen to generate the H2S. This hydrogen is primarily generated from the catalytic reforming unit.
- Now the question that are posed in the refinery are
- How to handle H2S for following environmental legislations
- How to purify the reformer H2 gas stream to meet the required inlet specifications in various hydrotreaters, hydrocracking and isomerisation units.
- How to produce H2 additionally, as the reformer off gas may not be able to meet the H2 demands in various hydrotreaters.
- When the above question is answered, in due course, we get the two major supporting processes
- Hydrogen production and purification process
- Sulfur recovery process. - We first discuss hydrogen production and purification process followed with the sulphur recovery process.
12.2 Hydrogen production
- Hydrogen can be produced in many ways namely
- Partial oxidation of heavy ends
- Steam reforming of various product stocks o Methane steam reforming.
- Amongst these, methane steam reforming is more famous for hydrogen production
- Depending upon the process, the hydrogen production consists of four basic reactions
- Reforming: Here, methane reacts with water molecules to form CO and H2 at about 20 bar and 800 oC. The reacton is endothermic.
- CO shift reaction: In this reaction, CO is converted to CO2 and H2 by reacting with water. The reaction is usually carried out on a catalyst. There are two types of shift reactions namely high temperature shift or low temperature shift. In the high temperature shift, the reaction iscarried out on iron oxide or chromia catalyst at about 350 – 550 oC. In the low temperature shift, the reaction is carried out at 200 – 250 oC using copper or zinc oxide on alumina.
- Gas purification: The CO2 is separated by passing the product gases through amine scrubber
- Methanation: The remaining CO2 and CO are converted back to methane using nickel-alumina catalyst in a reversible reaction scheme at 400 oC.
12.3 Hydrogen production technology ( Figure 12.1 )
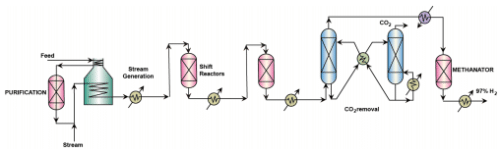
Figure 12.1 Flow sheet of Hydrogen Production Technology
- Feed purification: Feed pretreated to remove sulphur and halogens traces. H2S is removed using zinc oxide catalysts. Organic sulphur removed by hydrotreating and H2S removal from the feed. Halogens are removed using adsorption technique.
- Furnace reactor: The methane steam reforming reaction occurs in a furnace which is fed with the hydrocarbons mixed with steam. The steam to carbon ratio varies and is about 2.5 – 3.5. The furnace reactor consists of reactor tubes packed in the furnace chamber. The reactor tubes consist of the nickel oxide catalyst for carrying out the reaction.
- Shift reactors: The furnace reactor product is sent to both high temperature and low temperature shift reactors. It is interesting to note that these reactors operate at low temperatures. Therefore, cooling is carried out for the furnace reactor product and steam is generated. Similarly, steam is generated after the high temperature shift reactor also.
- Absorber stripper: The absorber stripper is used for CO2 removal of the product emanating from the low temperature shift reactor.
- Methanation reactor: Here, traces of the CO2 and CO are converted to CH4 and H2O using nickel catalyst and reversible reaction scheme. The product from methanation reaction consists of 97 % H2.
- Alternatively, in some modern refineries, the low temperature shift reactor product is fed to a pressure swing adsorption (PSA) unit which produces 99.9 % hydrogen as a main product.
- The PSA also produces a tail gas which is used as a fuel in the furnace used in the reformer process.
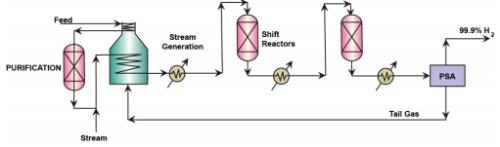
- PSA technology also is incapable for CO and CO2 removal as the adsorbents are not competent enough to separate these components to a large extent. But they can effectively do separation when hydrocarbons are present but not oxides in the hydrogen rich stream. Therefore, from PSA perspective as well it is important to remove CO2 bulk with amine scrubbing followed with methanation reaction for both CO and CO2 conversion.
12.4 Claus sulphur recovery process technology (Figure 12.3)
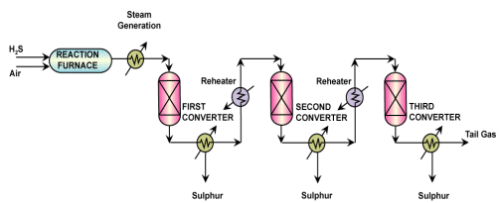
Figure 12.3 Flow sheet of Claus Sulphur Recovery Process Technology
- In a furnace reactor, H2S is partially oxided with air to produce water and SO2. The reaction is highly exothermic. Therefore, steam is generated using the products from the furnace reactor.
- The remaining H2S is then sent to a converter at about 250 oC to allow the reaction between H2S and SO2 and produce Sulfur and water. The emanating product is at 290 oC
- The second reactor (H2S to SO2) is having severe equilibrium limitations. Therefore, it is sent to two to three reactors for maximizing conversion.
- After each converter, the product stream is cooled and sent to another reactor. Subsequently, Sulphur is removed as a product from the coolers.
- Finally tail gas is obtained from the last converter which consists of unreacted H2S, N2 and O2.
- The tail gas requires treatment as well. This is because the gas consists of components such as H2S, CS2 etc. The tail gas is fed with air to another burner and converter that converts sulphur compounds to H2S.The H2S thus generated is separated using amine scrubbers. The H2S thus recovered is sent as a recycle stream to the partial oxidation reactor.
12.5 Technical questions
1. How good is conversion in the steam methane reforming reaction?
Ans: By maintaining good process conditions, the conversion of the methane steam reforming reaction can be achieved to about 60 – 80 % in a single furnace reactor. Therefore, a single furnace reactor is sufficient to achieve the desired conversion.
2. Why methanation cannot be avoided in the hydrogen production process?
Ans: The trace gases CO and CO2 are reactive towards the catalysts due to the presence of oxygen molecule. Therefore, H2 sent to various other units should be bereft of the CO and CO2 which can poison the catalyst due to the reactive oxygen molecule.
3. Why CO2 bulk removal is targeted in the hydrogen production process?
Ans: CO2 bulk production if avoided will affect the product quality. The methanation catalyst is not competent to fully convert CO2 back to methane due to the reversibility of the reaction. Therefore, CO2 removal is required.
4. What oppurtunites exist for heat integration in the hydrogen production process?
Ans: The feed to the process needs pre-heating therefore, is a cold steam. Now this stream can be integrated with the furnace itself where the combustion gases can be used to pre-heat the stream. Other than this the furnace product, high and low temperature shift reactor products are also available. The choice of heat integration and steam generation at various sites in the process is a complex optimization problem and has to be addressed by solving separate problems to finally arrive at the one optimal solution. Mostly, the furnace combustion gases will be integrated for energy recovery with the feed stream and steam generation is effected from the high and low temperature shift reactors.
5. Explain how using three reactors in series will enhance equilibrium conversion of the second conversion reaction i.e, H2S to S in Claus process?
Ans: Equilibrium conversion is a function of temperature and pressure. There are two types of equilibrium reactions namely exothermic and endothermic reactions. For exothermic reactions, the conversion increases with decreasing temperature. Therefore, after first converter, the product is cooled and sulphur is also removed. The reduction in temperature and elimination of sulphur moves the process conditions to a shift equilibrium to the right hand side. Therefore, series of chemical reactors followed with product cooling will enhance equilibrium conversion. By the by, the same concept is also used in hot and cold shot reactors. The only difference between this arrangement and the shot reactor arrangement is that there direct heat transfer by quenching or heating is allowed where as in the shown flow sheet, indirect heat transfer is facilitated only.
6. Why burner and converter are required in the tail gas processing unit?
Ans: The burner enhances the temperature of the stream and produce H2. The produced H2 reacts with sulphur compounds to thereby produce H2S.