Introduction
Gas absorption: It is a mass transfer operation in which one or more gas solutes is removed by dissolution in a liquid. The inert gas in the gas mixture is called “carrier gas”. In the absorption process of ammonia from air-ammonia mixture by water, air is carrier gas, ammonia is „solute” and water is absorbent. An intimate contact between solute gas and absorbent liquid is achieved in a suitable absorption equipment, namely, tray tower, packed column, spray tower, venture scrubber, etc. Desorption or stripping operation is the reverse of absorption. Absorption operation is of two types; physical and chemical.

4.1. Equilibrium solubility of gases in liquids
For the determination of driving force in any mass transfer operation, the solubility of a species in a solvent, i.e., equilibrium distribution between phases is important. With the increase in temperature, solubility of a gas in liquid decreases. Hence, absorption is done at lower temperature. On the contrary, desorption is done at higher temperature. The equilibrium characteristics of a gas-liquid system is discussed in chapter 3 (Mass Transfer Coefficient).
4.2. Selection of solvent for absorption and stripping
If the objective of absorption is separation of a particular component from a mixture, selection of absorbent plays a great role and when absorption operation is used to prepare a solution, solvent is selected according to final product. Few criteria for the selection of an absorbent are as follows:
(A) Gas Solubility: High solubility of a gas in the solvent is preferred, utilizing low quantity of solvent. Absorbent should not dissolve carrier gas. Similar chemical nature of solute and absorbent (solvent) gives a good solubility. If chemical reaction takes place between solute and solvent, rate of absorption is extremely high. But the reaction should be reversible to recover solvent during desorption.
(B) Volatility: Low volatility or low vapor pressure of the solvent enhances the adsorption operation as solvent loss with carrier gas is very small. Sometimes, a second less volatile solvent is used to recover the first solvent.
(C) Viscosity: For better absorption, a solvent of low viscosity is required. In mechanically agitated absorber, greater amount of power is required for high viscous solvent and flooding is also caused at lower liquid and gas flow rates.
(D) Corrosiveness: Non-corrosive or less corrosive solvent reduces equipment construction cost as well as maintenance cost.
(E) Cost: The solvent should be cheap so that losses will be insignificant and should be easily available.
(F) Toxicity and Hazard: The solvent should be non-toxic, nonflammable, non-hazardous and should be chemically stable.
Steam is generally used in desorption or stripping medium as stripped solute can be recovered very easily by condensing steam leaving desorption tower.
4.3. Design of single stage counter-current flow absorption tower (packed tower)
Two common gas absorption equipments are packed tower and plate tower. Other absorption equipments are, namely, spray column, agitated contactor, venture scrubber, etc. The gas and the liquid phases come in contact in several discrete stages. Thus, a stage wise contact is there in a plate column. But in packed tower, the up-flowing gas remains in contact with down-flowing liquid throughout the packing, at every point of the tower. Therefore, packed tower is known as “continuous differential contact equipment It is different from the stage-wise distillation column. In the stage distillation column the equilibrium in each stage will vary not in a continuous fashion whereas in the packed column the equilibrium is changed point wise in each axial location.
Steps for the design of packed tower
(A) Selection of solvent
(B) Selection of packing
(C) Calculation of minimum solvent flow rate as well as actual solvent flow rate
(D) Column diameter
(E) Height of column
(F) Design of solvent distributors and redistributors (if needed)
(G)Design of gas distributor, packing support, shell, nozzles, column support
(a) Equilibrium data; (b) gas and liquid flow rates; (c) solute concentration in two terminals; (d) individual and overall volumetric mass transfer coefficients should be known for the design of a packed absorption tower.
Packing Materials:
Packing materials are utilized to provide large interfacial area of contact between two phases. These are made from either of ceramics, metals or plastics. A number of packing materials with various size, shape and performance are available. These are classified into three types, namely, dumped or random, structured and grid.
The packing materials have following characteristics:
(a) Cost: The cost of the packing materials should be very low.
(b) Surface area: A large interfacial area of contact is always recommended. In that case, pressure drop will be more.
(c) Void volume: A high void volume is needed to maintain low pressure drop.
(d) Fouling resistance: Packing materials should not trap suspended solids present in liquid. Bigger packing materials generally give low fouling resistance.
(e) Mechanical strength: Good mechanical strength is desired for choosing packing materials as this will not break or deform during filling or operation.
(f) Uniform flow of streams: Stack of packing materials should have uniform void spaces through which both the streams (gas and liquid) can flow uniformly. Non-uniform flow of streams leads to stagnant liquid pool which in turn gives low mass transfer.
(A) Dumped or random packing materials: Dumped or random packing materials are classified into three categories as first generation (1907 to mid 1950); second generation (mid 1950 to mid 1970) and third generation (mid 1970 to till date). The first generation random packing materials are of three categories, such as, (a) Raschig rings; (b) Lessing rings and modified Raschig rings and (c) Berl saddles. These are shown in Figure 4.1.
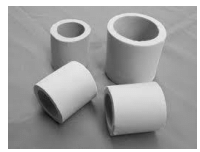
(a) Raschig rings;
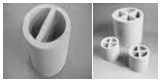
(b) Lessing rings and modified Raschig rings (Cross-partition rings)
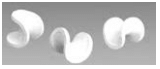
(c) Berl saddle Figure
4.1: First generation dumped or random packing materials
The second generation random packing materials are mainly (a) Intalox saddle and modification; (b) Pall ring and modification. Intalox saddle is the modified version of Berl saddle and offers less friction resistance due to particular shape (two saddles will never nest). Pall rings are modified version of Raschig rings. These are shown in Figure 4.2.
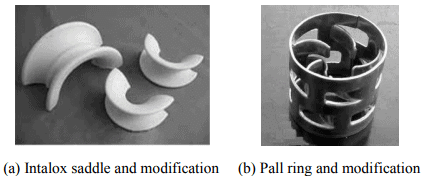
Figure 4.2: Second generation dumped or random packing materials.
The third generation random packing materials are numeral; (a) Intalox Metal Tower Packing (IMTP); (b) Nutter ring; (c) Cascade Mini-Ring (CMR); (d) Jaeger Tripac; (e) Koch Flexisaddle; (f) Nor-Pac; (g) Hiflow ring, etc. These are shown in Figure 4.3.
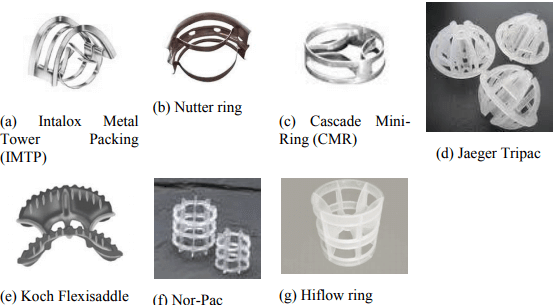
Figure 4.3: Third generation dumped or random packing materials.
(B) Structured packing materials:
These materials are used widely as packing materials in packed tower due to low gas pressure drop and improved efficiency. Corrugated metal sheet structured packing and Wire mesh structured packing materials are widely used in the industries. These include Mellapak, Flexipak, Gempak, Montz and MaxPak. These are shown in Figure 4.4.
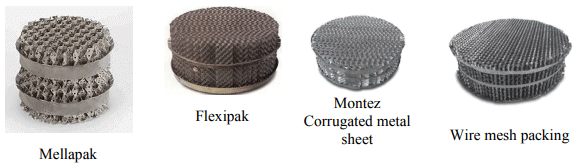
Figure 4.4: Snapshots of some structured packing materials.
(C) Grid packing materials:
This packing material is used for high gas or vapor capacities at low pressure drop.Mellagrid series; Flexigrid series; Snap grid series are among these grids. Figures 4.1-4.4 are taken from Google image.