Armature Resistance Control
- If external resistance Rg is inserted in series with armature resistance. By varying the external resistance Rg1 the speed is controlled. If Rg3 > Rg2 > Rg1 then speed is reduced from no-load speed as shown in figure
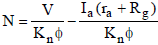
At no-load, Ia = 0, then no-load speed is
No = V/KnØ
- Using armature resistance control, speed can be control only below base speed. As flux remain constant at a constant current, say at rated current torque can be maintain constant, when speed is control. This is known as constant torque drive.
∴ Power = Torque × Speed
P = TN
if constant torque drive
then, for constant power drive
P = T × N
If speed is low then torque is high for constant power and when speed is high then torque is low. Hyperbolic characteristic.
Advantage
- This method controls speeds below base speed (rated speed) down to creeping speeds of only a few r.p.m., are easily obtainable. But at reduced speeds a considerable waste of energy. So this method is economically viable where only short time slow down are required.
Disadvantage
- Poor speed regulation with fixed controller resistance Rg in the armature circuit.
- Lower efficiency and operational cost is higher at reduced speed.
Field Flux Control
- Field current,
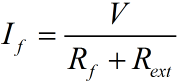
- Here, external resistance is inserted with field winding in series by varying external resistance Rext, field flux. We know very well that N ∝ 1/Ø
- The speed control is possible only above base speed. Above the base speed due to flux weakening higher current required to be drawn to maintain constant torque generally motor will not permitted to run beyond its rated current, so current is kept constant, hence torque will reduced. It means only constant power drive is applicable in this controlling scheme TN = constant.
Speed control by varying the armature terminal voltage
This is obtained by :
- Ward leonard system
- Controlled rectifiers
- Series-parallel armature control
Word-Leonard System
- In this system M is the main d.c. motor whose speed is to be controlled and G is the separately excited generator driven by a three-phase driving motor (usually an induction motor).
- Motor speed control is obtained nearly by changing the generator field current.
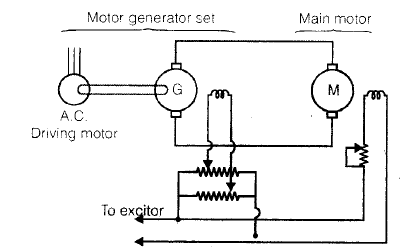
- In order to achieve wider speed control range speeds below base speed are obtained by armature voltage control and above base speed, by field flux control. For better utility of motor M, its armature current Ia is maintained equal to its rated current during its speed control.
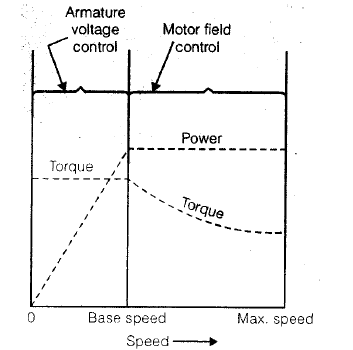
- Below base speed, constant torque drive, armature voltage control is applicable for suitable controlling. When both types of speed controls are employed, the overall speed range is 40 : 1.
Advantage
Disadvantage
TESTING OF D.C. MACHINES
- Machines are tested for finding out losses, efficiency and temperature rise. Direct loading tests may be performed on small machines. For large shunt machines, indirect machines are used. Swinburne’s test and Hopkinson’s test are mostly used in practice.
Swinburne’s Method
- This is the no-load test, it can not be performed on a d.c. series motor.
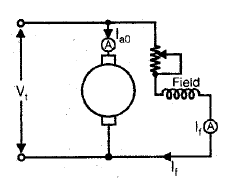
- In this method, the machine, whether it is a motor or a generator is run as no-load shunt motor at rated speed and rated terminal voltage Vt.
If
If = Field current
Ia0 = no-load armature current
The power absorbed by the armature
Vt Iao = No-load rotational losses
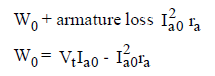
shunt field loss = Vt If
shunt field loss = VtIf
Let IL is the load current,
Then for generator efficiency
Armature current Ia = IL + If
Armature circuit loss =Ia2 ra
Shunt field loss =VtIf
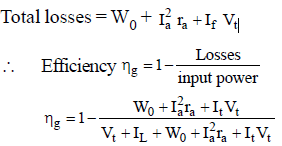
For motor efficiency,
When machine is working as a motor the Ia = IL – If
motor input = VtIL

Advantages
- Low power required for testing even large machines since only no-load losses are to be supplied from the mains.
- The efficiency of the machine can be calculated at any desired load.
Disadvantage
- No account is taken of the change in irion loss from no load to full load. At full load, due to armature reaction, flux is distorted which increases iron loss.
- As the test is on no load, it does not indicate whether the commutation on full load is satisfactory and whether the temperature rise would be within specified limits.
Hopkinson’s Method
- This test is also called.
- regenerative test
- heat run test
- back to back test
- Machine-I running as a motor drives machine-II as a generator. Since both the machines are coupled electrically, the power of generator-Ii is fed to the motor-I, it is for this reason that Hopkinson’s method is called regenerative method.
- The speed of the set should be equal to the rated speed.
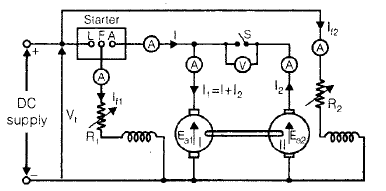
- I1 and I2 are armature currents of motor and generator respectively and Vt is the terminal voltage of both machines.
∴ Input to motor armature = VtI1
If ηm is the motor efficiency, then the output power = ηmVtI1
and if ηg is the generator efficiency,
then input of generator VtI2/ηg
VtI2 = generator output.
Since the generator is driven by motor, from figure Motor output = generator input
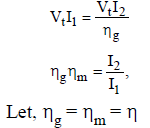
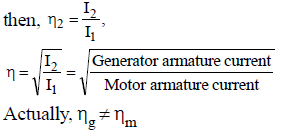
Because,
- The motor armature current I1 = I + I2 is greater than generator armature current I2. So armature losses are more in motor than generator.
- The generator field current If2 > motor field current at constant rated speed, iron losses (α speed and flux) is more than motor in generator.
So, efficiency are calculated on consideration of above two reason.
So, no-load rotation loss = Power drawn from the supply-armature losses in both.

where,
ram = armature resistance of motor and
rag = armature resistance of generator
No-load rotational loss for each machine = Wo/2
when we assume in both case no-load rotational loss are same.


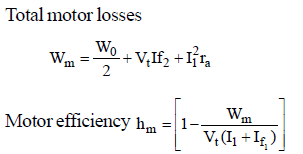
Advantage
- The total power taken from the supply is very low. Therefore this method is very economical.
- Temperature rise and the commutation conditions can be checked under rated condition.
- Stray losses are considered in both machines.
- Efficiency at different loads can be determined.
Disadvantage
- Two identical d.c. machines requirement. Consequently, this test is suitable for manufactures of large d.c. machines.
Field’s test for Series Machines
- In this method, two identical d.c. series machines are required which are then mechanically and electrically coupled together. This test gives efficiencies of both the machines.
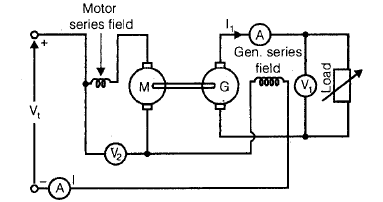
- The iron losses are same in both machines because the series fields of both M and G are connected in series with the motor armature. In order that load is not thrown off accidently, the generator armature is connected to load directly without any switch.
- This method is not regenerative method, because the generator output is wasted in load resistance and not fed to the motor
Let,
Vt = supply voltage
I = motor input current
V1 = generator terminal voltages
I1 = generator output current
Power input to whole set = VtI
Power output of the generator = V1I1
Total losses in the whole set, W = VtI – V1I1
Total ohmic losses,
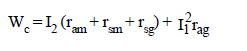
where,
ram = motor armature resistance
rag = generator armature resistance
rsg = generator series field resistance etc.
No-load rotational loss of both the machines.
∴ No-load rotational loss of each machine Wo/2
Motor power input = V2I
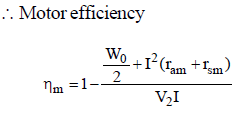

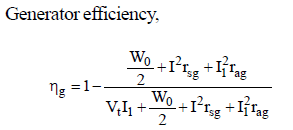
- At the same time, there is no-difficulty in obtaining two similar d.c. series machines, because these motors used for traction purposes are usually available in pairs.(on the basis of characteristics).