Chapter 7: Concrete
Workability:-
It is the property of concrete by virtue of which it can be easily mixed, transported, placed compacted, and finished. It may also be defined as the amount or useful internal work required to be done by concrete in order to achieve full compaction.
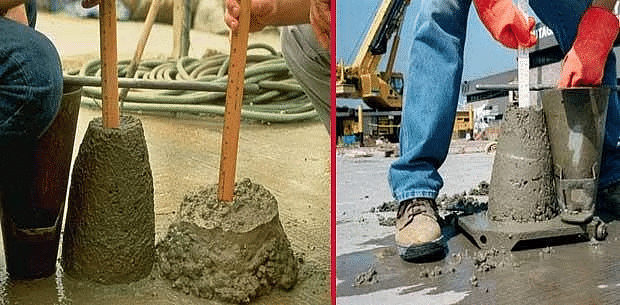
Workability of Concrete:-
The workability of concrete is the property of freshly mixed concrete which determines the ease and homogeneity with which it can be mixed, placed, consolidated, and finished.
It depends upon the following factors:–
a) Water Content: The water/cement ratio is one of the most important factors that influence concrete workability. Generally, a water-cement ratio of 0.45 to 0.6 is used for good workable concrete without the use of any admixture. The higher the water/cement ratio, the higher will be the water content per volume of concrete and the concrete will be more workable. Higher water/cement ratio is generally used for manual concrete mixing to make the mixing process easier. For machine mixing, the water/cement ratio can be reduced. These generalised methods of using water content per volume of concrete is used only for nominal mixes. For designed mix concrete, the strength and durability of concrete is of utmost importance and hence water water-cement ratio is mentioned with the design. Generally designed concrete uses a low water/cement ratio so that desired strength and durability of concrete can be achieved.
b) Mix Proportion:– Mix proportion of concrete tells us the ratio of fine aggregates and coarse aggregates w.r.t. cement quantity. This can also be called as the aggregate cement ratio of concrete. The more cement is used, concrete becomes richer and aggregates will have proper lubrications for easy mobility or flow of aggregates.
The low quantity of cement w.r.t. aggregates will make the less paste available for aggregates and mobility of aggregates is restrained.
c) Shape of aggregate:– The shape of aggregates affects the workability of concrete. It is easy to understand that rounded aggregates will be easier to mix than elongated, angular and flaky aggregates due to less frictional resistance.
d) Size of aggregate:–Surface area of aggregates depends on the size of aggregates. For a unit volume of aggregates with large sizes, the surface area is less compared to the same volume of aggregates with small sizes.
When the surface area increases, the requirement of cement quantity also increases to cover up the entire surface of aggregates with paste. This will make more use of water to lubricate each aggregate.
Hence, smaller sizes of aggregates with the same water content are less workable than large aggregates.
e) Grading of aggregate:–
Grading of aggregates have the maximum effect on the workability of concrete. A well graded aggregates have all sizes in required percentages. This helps in reducing the voids in a given volume of aggregates.
The less volume of voids makes the cement paste available for aggregate surfaces to provide better lubrication to the aggregates.
Measurement of Workability:–
The workability of the concrete can be measured by any of the following test:
(1) Slump test
(2) Compaction factor test
(3) Flow table test
(4) Vee-bee consistometer test
(1) Slump test:–
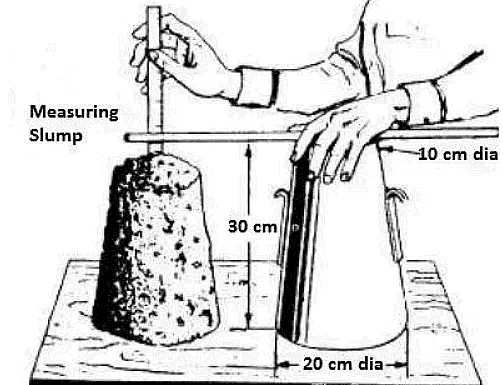
- It is the most common test that is used to measurement for the workability of concrete.
- It consists of a mould that is in the form of frustum having a top dia of 10cm, bottom dia of 20cm & ht. of 30 cm.
- The concrete to be tested is filled in this mould in 4 layers where in each layer is compacted 25 times with the help of the rod.
- After the mould is completely filled it is lifted immediately in vertically upward direction which causes the concrete to subside & the subsidence of the concrete is referred as slump which may also be defined as the difference level of the ht. of mould & the highest point of subsided concrete.
- The slump of the concrete represents its workability as higher is the value of slump higher its workability.
- This test is not suitable for concrete that either possesses very high workability or very low workability.
(2) Compaction factor test:
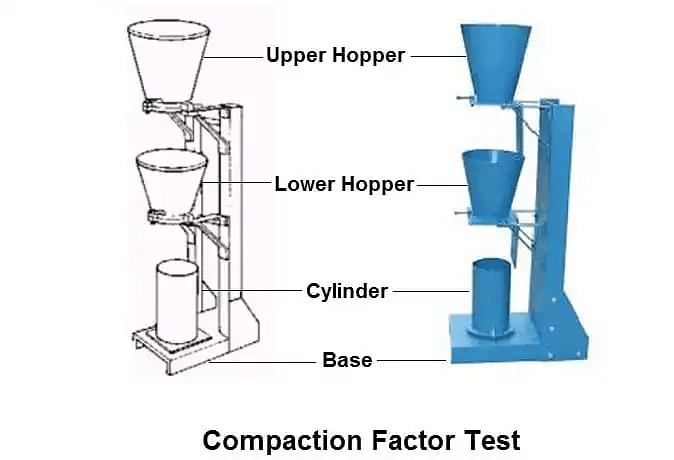
- This test is used to find the workability of the concrete for which its value is comparatively low. Hence, slump test is not suitable.
- The principle of this test is based upon determining the degree of compaction achieved by the amount of work done by allowing the concrete to fall through standard height.
- The degree of compaction is represented in terms of compaction factor, that represents density ratio that is density of the fully compacted concrete.
- The results obtained from compaction factor test are more uniform than those obtained from slump test.
- Compaction factor: The compaction factor test is the workability test for concrete conducted in laboratory. The compaction factor is the ratio of weights of partially compacted to fully compacted concrete. The Compaction factor values ranges from 0.7 to 0.95.
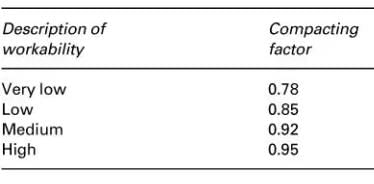
(3) Flow Table Test :—
- This test is performed for the concrete which posses very high workability.
- It consists of a circular table 76 cm in dia & a mould is in the form of frustum having the top dia of 17 cm & bottom dia of 25 cm & ht. of 12 cm.
- Concrete to be tested is filled in the mould in two layers that is placed over the flow table, when the mould is completely filled, it is removed immediately & the table is raised & dropped by 12.5 mm, 15 times in 15 sec.
- The spread of the concrete on the table is noted in at least 6 direction that is further used to represent its workability.
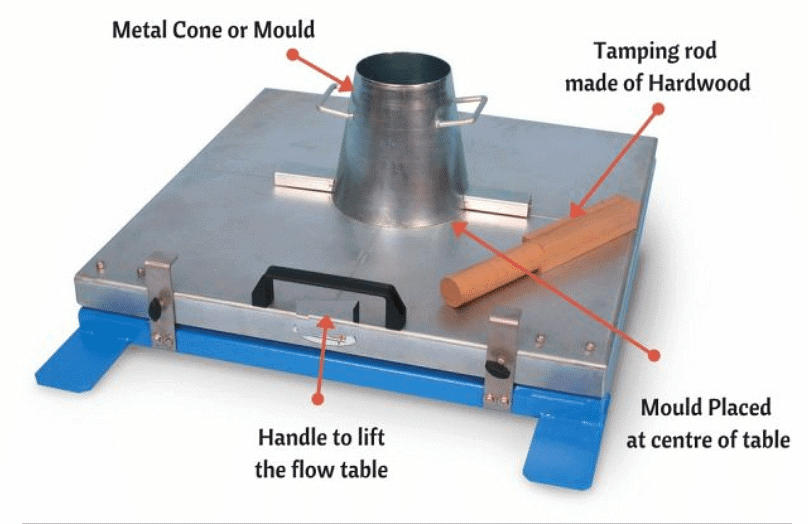
(5) Vee-bee Consistometer test :
- This test is used to find workability of slump concrete less than 50 mm.
- It consists of a mould in the form of the frustum that is placed inside the cylinder which is further placed over the vibrating table.
- Concrete to be tested id filled in the mould which is raised immediately & cylinder is subjected to vibration.
- The time required by the concrete to assume the cylindrical shape is noted that is referred as Vee-bee degrees & is further used to represents the workability of the concrete
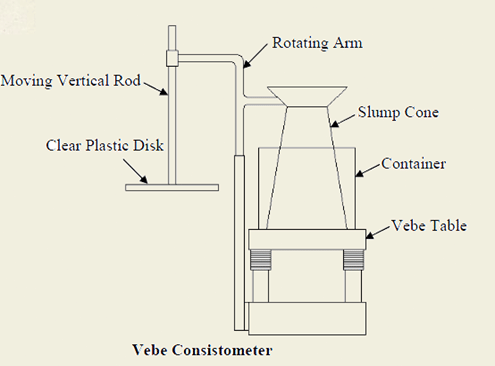
|
Download the notes
Concrete
|
Download as PDF
|
Strength:
(i) Compressive Strength:–
- Remove the specimen from water after specified curing time and wipe out excess water from the surface.
- Take the dimension of the specimen to the nearest 0.2m
- Clean the bearing surface of the testing machine
- Place the specimen in the machine in such a manner that the load shall be applied to the opposite sides of the cube cast.
- Align the specimen centrally on the base plate of the machine.
- Rotate the movable portion gently by hand so that it touches the top surface of the specimen.
- Apply the load gradually without shock and continuously at the rate of 140 kg/cm2/minute till the specimen fails
- Record the maximum load and note any unusual features in the type of failure.
(ii) Tensile Strength Test:
- Tensile strength is an important property of concrete because concrete structures are highly vulnerable to tensile cracking due to various kinds of effects and applied loading itself.
- However, tensile strength of concrete is very low in compared to its compressive strength.
- Due to difficulty in applying uniaxial tension to a concrete specimen, the tensile strength of the concrete is determined by indirect test methods: (1) Split Cylinder Test (2) Flexure Test.
(iii) Split-Cylinder Test:
- A standard test cylinder of concrete specimen (300 mm X 150mm diameter) is placed horizontally between the loading surfaces of Compression Testing Machine.
- The compression load is applied diametrically and uniformly along the length of cylinder until the failure of the cylinder along the vertical diameter.
- To allow the uniform distribution of this applied load and to reduce the magnitude of the high compressive stresses near the points of appplication of this load, strips of plywood are placed between the specimen and loading platens of the testing machine.
- Concrete cylinders split into two halves along this vertical plane due to indirect tensile stress generated by poisson's effect.
- Due to this compressive loading, an element lying along the vertical diameter of the cylinder is subjected to a vertical compressive stress and a horizontal stress.
- The loading condition produces a high compressive stress immediately below the loading points. But the larger portion of cylinder, corresponding to its depth is subjected to uniform tensile stress acting horizontally.
- It is estimated that the compressive stress is acting for about 1/6 depth and the remaining 5/6 depth is subjected to tension due to poisson's effect.
- Assuming concrete specimen behaves as an elastic body, a uniform lateral tensile stress of ft acting along the vertical plane causes the failure of the specimen, which can be calculated from the formula as,
|
Take a Practice Test
Test yourself on topics from Civil Engineering (CE) exam
|
Practice Now
|
Non-Destructive Test:
- Non destructive test is a method of testing existing concrete structures to assess the strength and durability of concrete structure.
- In the non destructive method of testing, without loading the specimen to failure (i.e. without destructing the concrete) we can measure strength of concrete.
- This method of testing also helps us to investigate crack depth, micro cracks and deterioration of concrete.
- Non destructive testing of concrete is a very simple method of testing but it requires skilled and experienced persons having some special knowledge to interpret and analyze test results.
(1) Schmidt Rebound Hammer Test:—
- Procedure for a rebound hammer test on concrete structure starts with calibration of the rebound hammer.
- For this, the rebound hammer is tested against the test anvil made of steel having Brinell hardness number of about 5000 N/mm2.
- After the rebound hammer is tested for accuracy on the test anvil, the rebound hammer is held at right angles to the surface of the concrete structure for taking the readings.
- The test thus can be conducted horizontally on vertical surface and vertically upwards or downwards on horizontal surfaces.
- If the rebound hammer is held at intermediate angle, the rebound number will be different for the same concrete.
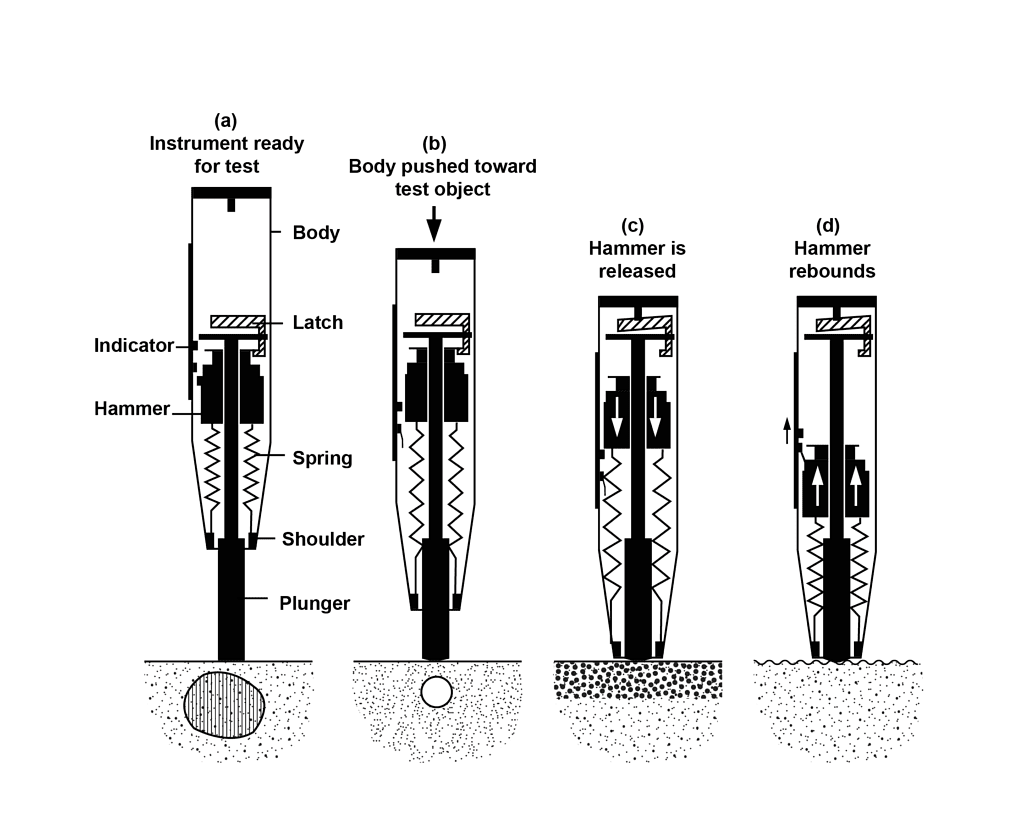
(2) Ultrasonic Pulse Velocity Test :–
- This test deals with the measurement of time of travel of electronically generated mechanical pulse through the structure that is further used to find the velocity of pulse that represents the quality of the structure to be tested.
- In this test the mechanical pulse is generated with the help of electroacoustic transducer and is detected with the help of transmitter.
- The time is noted between the formation of the pulse and its detection through a known distance from the structure.
- Generally, three types of arrangements are used for the direct transmission. (1) Direct transmission (2) Semi-direct transmission (3) Surface transmission
- Quality of the concrete is related to the structure as below:–
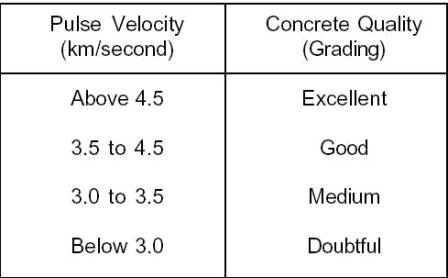