Arc blow is a welding defect which is encountereda)In arc welding usin...
Arc blow is basically a deflection of a welding arc from its intended path i.e. the axis of the electrode. Deflection of the arc during welding reduces the control over the handling of molten metal by making it difficult to apply the molten metal at right place. Arc blow is mainly encountered during DC arc with straight polarity welding due to an interaction between different electromagnetic fields in and around the welding arc.
Types of Arc blow:
- Forward Arc Blow
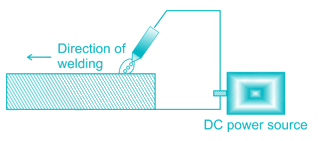
- Backward Arc Blow
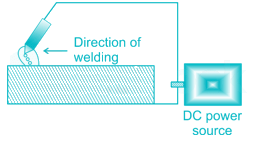
View all questions of this test
Arc blow is a welding defect which is encountereda)In arc welding usin...
Arc blow is a welding defect which is encountered in arc welding using DC current.
Explanation:
Arc blow is a common welding defect that occurs during the arc welding process. It refers to the deflection or deviation of the electric arc from its intended path. This can result in an irregular and inconsistent weld bead, which can weaken the joint and compromise the overall quality of the weld.
Causes of Arc Blow:
Arc blow is primarily caused by the magnetic field generated by the electric current flowing through the welding circuit. The magnetic field interacts with the arc and the surrounding metal, causing the arc to be pushed away from its intended direction. This can be influenced by several factors, including:
1. Magnetic properties of the base metal: Some metals, such as carbon steel, have higher magnetic permeability than others. This means they are more susceptible to the effects of the magnetic field and are more likely to experience arc blow.
2. Improper grounding: Inadequate grounding of the workpiece or the welding equipment can contribute to arc blow. The grounding provides a complete circuit for the electric current, and any disruptions or inconsistencies in the grounding can cause the magnetic field to be unevenly distributed, leading to arc blow.
3. Incorrect electrode positioning: The position of the electrode relative to the workpiece can also affect arc blow. If the electrode is not properly aligned with the joint or if it is too far from the workpiece, the magnetic field can exert a greater influence on the arc, causing it to deviate.
DC Current and Arc Blow:
Arc blow is most commonly encountered in arc welding processes that use direct current (DC) power sources. With DC current, the electric current flows continuously in one direction, creating a steady magnetic field. This magnetic field interacts with the arc and the surrounding metal, increasing the likelihood of arc blow.
On the other hand, in arc welding using alternating current (AC), the direction of the current changes periodically, resulting in a constantly changing magnetic field. This can help to mitigate the effects of arc blow, as the magnetic field is less likely to cause a consistent deflection of the arc.
Therefore, the correct answer to the question is option 'B' - Arc blow is encountered in arc welding using DC current.
To make sure you are not studying endlessly, EduRev has designed Railways study material, with Structured Courses, Videos, & Test Series. Plus get personalized analysis, doubt solving and improvement plans to achieve a great score in Railways.