Introduction
Inventory control encompasses the management of various types of inventory, including raw materials, stored supplies, spare parts, partly finished goods, and finished goods. Its primary objective is to ensure the availability of the required quantity of inventory, maintaining the necessary quality, and delivering them at the specified time while minimizing the capital investment. Efficient inventory turnover is pursued to maximize turnover while adequately stocking to meet demand. The determination of inventory levels considers factors such as available finance, discounts, storage costs, and available space.
Techniques of Inventory Control
Several techniques are employed for effective inventory control:
- ABC Analysis: This method involves categorizing inventory into three groups based on their value and consumption. 'A' items represent high-value items with significant consumption, 'C' items are low-value items with minimal consumption, and 'B' items fall in between. ABC analysis allows for selective control over inventory, focusing attention and resources where they are most needed.
ABC Analysis
ABC analysis is crucial for strategic inventory management. By identifying and prioritizing items based on their value and consumption, businesses can allocate resources efficiently. This analysis involves several steps:
- Calculation of Unit Cost and Usage: Determine the unit cost and usage of each item over a specific period.
- Determination of Net Value: Multiply the unit cost by the estimated usage to obtain the net value of each item.
- Ranking by Value: List all items by their annual consumption value and arrange them in descending order.
- Percentage Calculation: Accumulate the total value and number of items, then calculate the percentage of total inventory value and quantity.
- Curve Representation: Plot a curve showing the percentage of items and their corresponding value.
- Classification into Categories: Determine rational limits for categorizing items into A, B, and C based on the curve representation.
ABC analysis aids in focusing attention on critical inventory items while minimizing resources allocated to less significant items. It helps in identifying obsolete stocks, reducing clerical costs, and improving inventory turnover, ultimately enhancing overall inventory management efficiency.
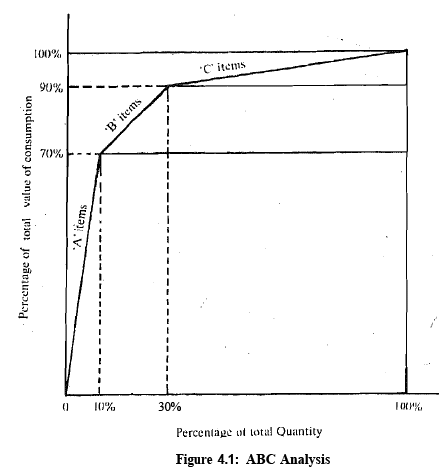
Question for Inventory Control
Try yourself:
What is the purpose of inventory control?Explanation
- Inventory control is implemented to ensure that the required quantity of inventory is available when needed.
- It aims to maintain the necessary quality and deliver the inventory at the specified time.
- By effectively managing inventory, businesses can meet customer demand and avoid stockouts or overstocking.
- The primary objective of inventory control is to balance inventory levels to minimize capital investment while ensuring the availability of inventory to fulfill customer orders.
- It involves considering factors such as available finance, discounts, storage costs, and available space to determine optimal inventory levels.
Report a problem
Understanding Stock Levels in Inventory Control
Importance of Stock Levels
Maintaining an optimal stock level is crucial for effective inventory management. Overstocking leads to excessive investment, space constraints, and risks of quality deterioration, while understocking results in frequent purchases, higher costs, and production losses. Therefore, establishing appropriate stock levels is essential to strike a balance between these extremes.
Fixed Levels in Inventory Control
The stores department employs scientific techniques to manage materials efficiently, including the fixation of certain levels for each item:
- Minimum Stock Level: Represents the threshold below which the stock should not fall to avoid disruptions in production. Factors considered include lead time and consumption rate during that period.
- Maximum Stock Level: Sets the upper limit of stock to prevent overstocking and associated costs and risks.
- Re-ordering Level: Indicates the point at which the storekeeper initiates a requisition for purchasing fresh supplies. It typically lies between the minimum and maximum stock levels, considering lead time, consumption rate, and economic ordering quantity.
- Danger Level: Marks a critical point where immediate action is required to avoid stockouts.
Calculating Re-ordering Level
The re-ordering level can be calculated using either of the following formulas:
- Re-order level = Maximum consumption × Maximum re-order period
- Re-order level = Minimum level + consumption during the time required to get fresh deliveries
Illustration 1:
Given:
Maximum consumption: 400 units per week
Re-order period: 4 to 6 weeks
Ans: Re-order level = 400 × 6 = 2,400 units
Illustration 2:
Given:
Maximum stock: 2,500 units
Minimum stock: 1,000 units
Time required for receiving material: 10 days
Daily consumption: 50 units
Ans: Re-order level = 1,000 + (50 × 10) = 1,500 units
Minimum Stock Level
This indicates the minimum quantity of an item to be maintained at all times to prevent production disruptions. It is calculated using the formula:
- Minimum stock level = Re-order level - (Normal consumption × Normal re-order period)
- Factors considered in fixing this level include lead time, consumption rate, and re-order level.
Understanding Maximum Stock Level and Other Stock Levels
Importance of Maximum Stock Level
The maximum stock level denotes the upper limit of material stock that should not be exceeded. Fixing this level aims to prevent overinvestment in stock and ensure efficient utilization of working capital. Various factors influence the determination of the maximum stock level, including available working capital, consumption rate, delivery time, storage space, economic ordering quantity, inventory carrying costs, risk of loss due to deterioration or price fluctuations, and potential changes in fashion or specifications.
Calculation of Maximum Stock Level
The following formula is commonly used to calculate the maximum stock level:
Maximum stock level = Re-order level + Re-order quantity - (Minimum consumption × Minimum re-order period)
Danger Level
The danger level signifies a critical stock level below the minimum level. When inventory reaches this point, immediate action is required to replenish stock to avoid production disruptions. At this level, no further issues are made without special approval, and calculations often consider the time needed for emergency purchases.
Average Stock Level
The average stock level is calculated using the formula:
- Average stock level = (Minimum stock level + Maximum stock level) / 2
- Alternatively, it can be computed based on available information:
- Average stock level = Minimum stock level + (2 × Re-order quantity)
Illustration 3: Calculation of Stock Levels
Given:
- Re-order quantity: 30,000 units
- Delivery time: 2-4 months
- Maximum consumption: 8,000 units per month
- Normal consumption: 5,000 units per month
- Minimum consumption: 3,000 units per month
Ans:
Re-ordering level = 8,000 × 4 = 32,000 units
Minimum stock level = 32,000 - (5,000 × 3) = 17,000 units
Maximum stock level = 32,000 + 30,000 - (3,000 × 2) = 56,000 units
Understanding Re-Order Quantity (ROQ) and Economic Order Quantity (EOQ)
Re-Order Quantity (ROQ)
- The re-order quantity, also known as the economic order quantity (EOQ), refers to the predetermined amount of materials that the storekeeper purchases when the stock reaches the re-order level.
- It is essential to ensure that upon receiving the ordered quantity, the stock level does not surpass the maximum level allowed at any given time. The term "economic order quantity" emphasizes the economic efficiency of ordering this specific quantity of materials.
Economic Order Quantity (EOQ)
- The economic order quantity is determined based on the principle of minimizing costs associated with ordering and carrying inventory. Ordering materials in quantities larger than the economic order quantity increases carrying costs, including expenses such as interest on investment, obsolescence, space utilization, storage charges, insurance, and personnel costs.
- Conversely, purchasing small quantities frequently leads to increased ordering costs due to extra purchasing, handling, transportation costs, and the potential for stockouts, which disrupt production schedules and incur additional expenses like overtime and loss of sales and goodwill.
Question for Inventory Control
Try yourself:
What is the purpose of establishing appropriate stock levels in inventory management?Explanation
- Establishing appropriate stock levels is crucial in inventory management to strike a balance between overstocking and understocking.
- Overstocking leads to excessive investment, space constraints, and risks of quality deterioration.
- Understocking results in frequent purchases, higher costs, and production losses.
- Therefore, maintaining optimal stock levels helps in minimizing costs, preventing disruptions in production, and ensuring efficient utilization of working capital.
Report a problem
Calculation of Economic Order Quantity
The economic order quantity can be calculated using the following formula:
Where:
- EOQ = Economic order quantity
- U = Annual usage in units
- O = Cost of placing one order, including receiving costs
- I = Cost of carrying one unit of inventory for one year
This formula determines the optimal order quantity that minimizes the total costs associated with ordering and carrying inventory, ensuring efficiency in inventory management and cost-effectiveness in procurement practices.
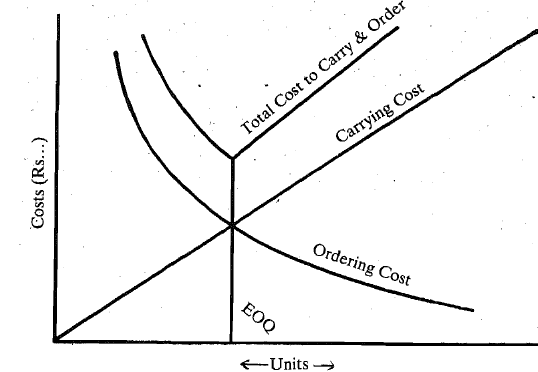
The calculation of economic order quantity is subject to the following conditions:
- The quantity of the item to be consunled during a particular period is known.
- Cost per unit is known and is constant. Further quantity discounts are not involved
- Ordering cost and carrying cost are known. They are fixed per unit and will remain the same throughout
- Quantity ordered is delivered immediately. The following illustration will explain - to you the calculation of economic order quantity.
Illustration 4
From the following particulars calculate the economic order quantity
- Annual usage = 6,000 units,
- Cost of the material per unit = Rs. 2.50
- The cost of placing and receiving one order = Rs. 15.00
- Annual carrying cost of one unit = 20% of inventory value
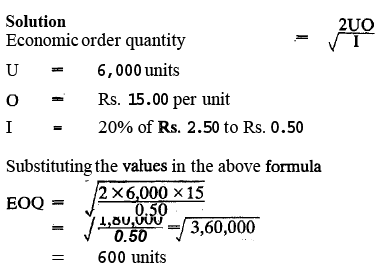